Shift down a gear. Browse and enjoy.
Exclusive, unique, inspiring: Christophorus is the magazine for Porsche enthusiasts. And almost as old as the sports car brand itself. Ever since the first issue in 1952, the publication has been inspiring its readers with stories about the Porsche company – with personalities, products, history, and motorsport.
The print edition of the Porsche magazine is published four times a year in 11 languages worldwide, with a print run of around 600,000 copies per issue. Christophorus is considered one of the most prestigious corporate magazines worldwide. Historical copies are highly collectible.



Issue #414
A Modern Classic
Luca Trazzi made his dream of a 911 Speedster based on generation 993 come true. Three years of close collaboration with Porsche resulted in the first-ever Sonderwunsch factory one-off for a specific customer. Christophorus paid him a visit.
9:11 – the video magazine
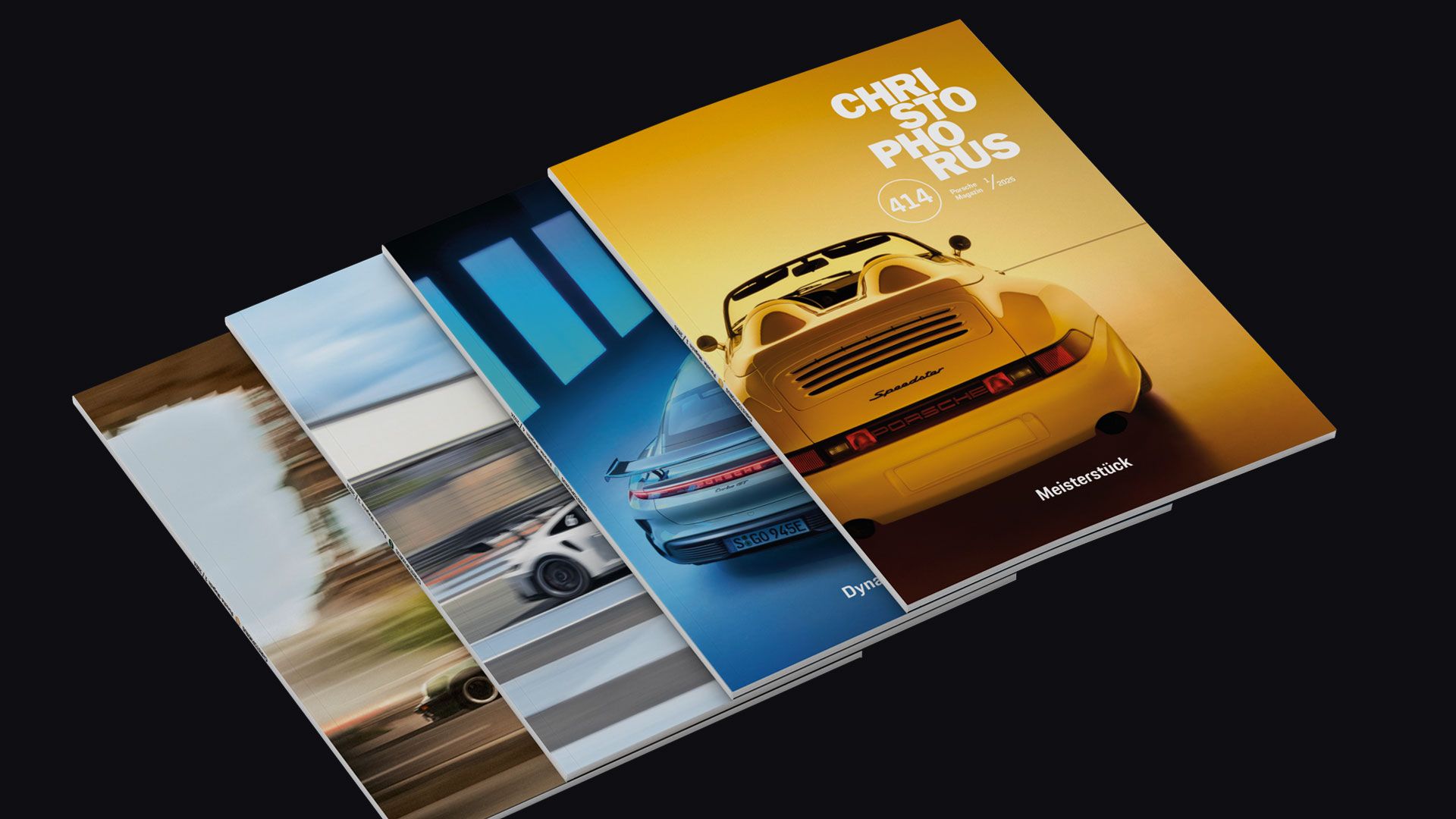
Subscribe
Four issues of Christophorus are published each year; available by subscription for 24 euros.