Shift down a gear. Browse and enjoy.
Exclusive, unique, inspiring: Christophorus is the magazine for Porsche enthusiasts. And almost as old as the sports car brand itself. Ever since the first issue in 1952, the publication has been inspiring its readers with stories about the Porsche company – with personalities, products, history, and motorsport.
The print edition of the Porsche magazine is published four times a year in 11 languages worldwide, with a print run of around 600,000 copies per issue. Christophorus is considered one of the most prestigious corporate magazines worldwide. Historical copies are highly collectible.
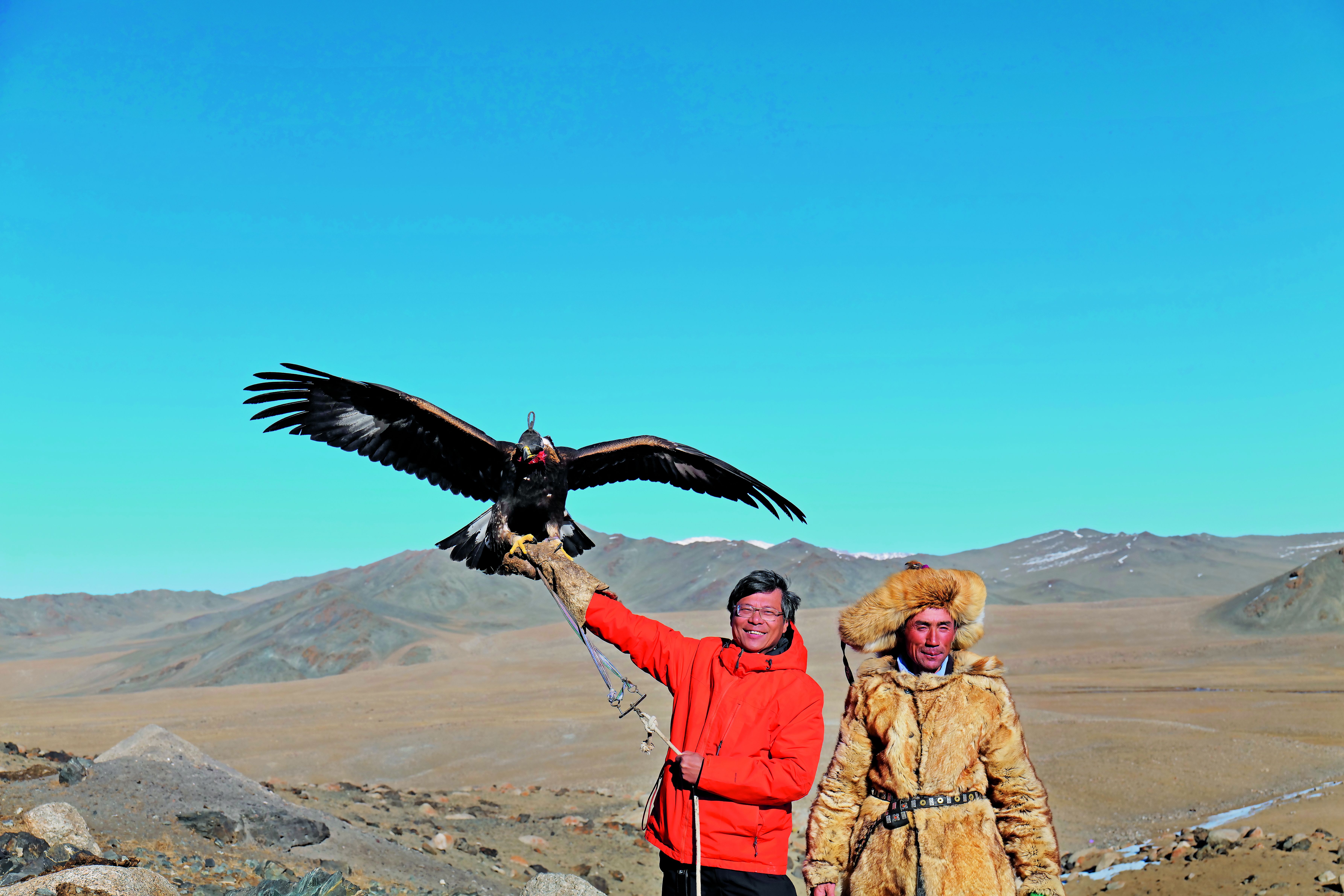
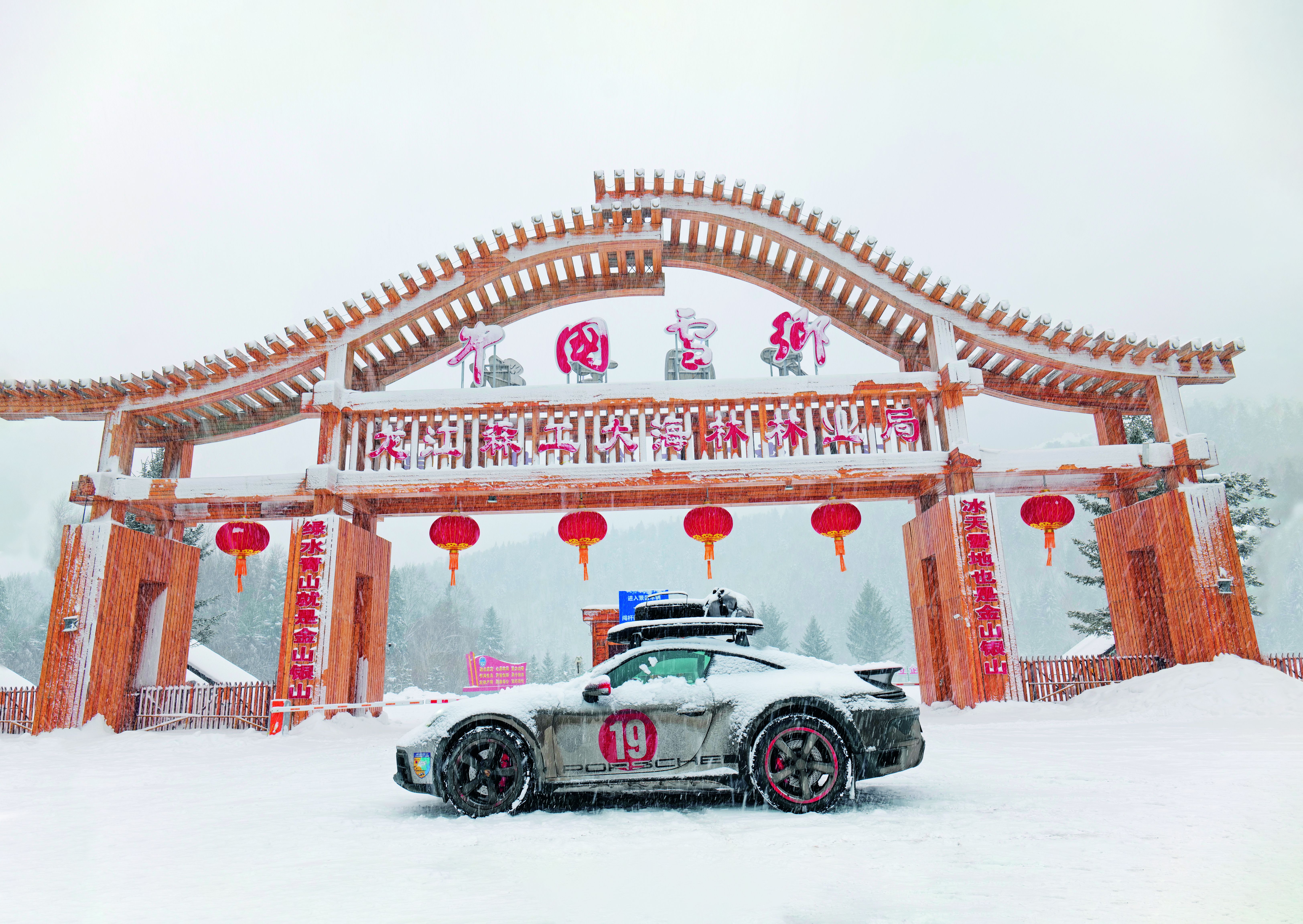

Issue #413
Diary from the desert.
From negative 20 to positive 38 degrees Celsius, from the coast to an elevation of nearly 4,700 meters, and from highways to gravel roads, Nguyen Hoang Anh, owner of a logistics company, drove his 911 Dakar from Vietnam to the Mongolian part of the Gobi Desert and back again.
9:11 - the video magazine

Subscribe
Four issues of Christophorus are published each year; available by subscription for 24 euros.