La perfection dans la Construction
Comme toutes les
Un soubassement qui invite à la danse. Au poste 1810 du nouvel atelier de tôlerie de l’usine
Il n’était jusqu’alors qu’une accumulation de pièces d’aluminium et d’acier livrées par les équipementiers au centre d’approvisionnement de l’atelier de tôlerie. De là, chaque élément est acheminé en temps voulu par des trains de remorques jusqu’à la ligne de fabrication. Ces installations ont été construites en un temps record : moins de 26 mois pour bâtir les ateliers de tôlerie et de peinture, mais aussi pour transformer l’atelier de montage, sans interrompre l’activité. La surface de production est passée de 79 900 m² à un total de 245 900 m², soit environ 34,5 terrains de football. Une performance applaudie par Oliver Blume, membre du Directoire en charge de la production : « Je suis ravi de la manière dont l’équipe a géré les choses. »
Le premier des trois robots a troqué sa pince à souder contre une pince préhensile, avec laquelle il soulève le bas de la caisse du
Le processus en question débute à l’usine Volkswagen de Bratislava, en Slovaquie. C’est là que la plus grande presse du groupe VW réalise l’emboutissage du capot du
Retour à Leipzig. Dernier poste de l’atelier de tôlerie, la finition. Deux tôliers contrôlent les surfaces et chacune des pièces. « La géométrie du véhicule doit être correcte pour que tout tombe parfaitement au montage », explique Thomas Riediger. Les caisses s’éloignent maintenant vers l’atelier de peinture.
Galerie.
L’usine de Leipzig allie une production de série ultramoderne au soin haut de gamme d’une manufacture. Mot d’ordre : personnalisation. « Nous pouvons par exemple appliquer n’importe quel coloris extérieur choisi par le client », précise Roland Töpfer, qui dirige l’atelier de peinture. « C’est la fonction de notre ‘sofa’. » Ce petit nom désigne un système capable de préparer la quantité de peinture nécessaire pour un seul véhicule, et de changer si besoin de couleur à chaque fois.
Mais tout d’abord, c’est l’heure du bain. Avant la cataphorèse, la caisse est débarrassée de toute impureté et trace de graisse. Puis le
Une fois les soudures et les jonctions (les points de liaison) étanchéifiées et la protection du dessous de caisse réalisée, place à la couleur. Apprêt, laque de base, laque transparente : voilà l’ordre dans lequel chaque
L’usine
Le tunnel Ergo Lux, équipé de modules LED à faible consommation, s’inscrit aussi dans cette démarche. Ses raies de lumière ultra précises permettent un contrôle optimal de la peinture. Deux collaborateurs scrutent avec concentration un capot et en effleurent délicatement la surface à main nue. C’est la seule façon de sentir les irrégularités nécessitant un polissage. Le
On est d’abord frappé par l’aisance déconcertante du processus. Les caisses sont suspendues à des convoyeurs et pivotent dans les airs, ou passent d’un poste à l’autre grâce à des plateformes élévatrices. Des trains de remorques électriques se croisent, approvisionnant la ligne de montage en matériel. Un ballet réglé comme du papier à musique, qui semble obéir à un ordre supérieur. C’est que tout est régi par un processus logistique reposant sur l’absence de stocks et visant à acheminer chaque pièce « juste à temps » et « juste en séquence ». Mais les collaborateurs donnent eux aussi cette impression d’aisance. L’extension de l’usine a conduit à l’embauche de 1 500 personnes, chacune qualifiée et intégrée à l’équipe. « Travailler pour
Avant la ligne Dessous de caisse, le
Indispensable tout au long de la chaîne de création de valeur, le contrôle qualité obéit au principe du zéro défaut : « jamais réceptionner d’erreur, jamais faire d’erreur, jamais transmettre d’erreur », telle est la devise. C’est pour garantir cette qualité que
Une fois sorti de la ligne Dessous de caisse, le
Tandis que la caisse avance suspendue à sa balancelle, le train de roulement et le groupe propulseur se rapprochent sur un véhicule autoguidé (AGV). L’union solennelle de la voiture est entièrement automatisée. Les témoins se trouvent un poste plus loin, pour visser les jambes de force à leur support. En guise de trousseau, le
Oliver Blume connaît de première main tous les processus de production du
Texte Thorsten Schönfeld
Photos Stefan Warter
Pour la production du
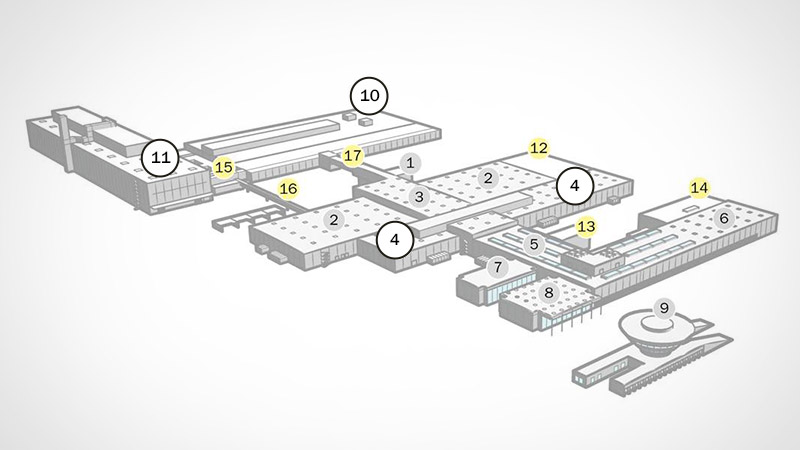
USINE CENTRALE
1 Terminal de déchargement
2 Centre d’approvisionnement
3 Module de découplage
4 Ligne de montage
5 Montage final
6 Centre de pilotage et d’analyse
7 Cafétéria
8 Centre d’intégration
9 Centre Clients
NOUVEAUX ATELIERS
10 Atelier de tôlerie
11 Atelier de peinture
12 Annexe au centre d’approvisionnement
13 Nouveau prémontage des moteurs
14 Nouvelle ligne de finition
15 Centre d’intégration Ouest
16 Passerelle Piétons
17 Passerelle Tôlerie
Atelier de tôlerie
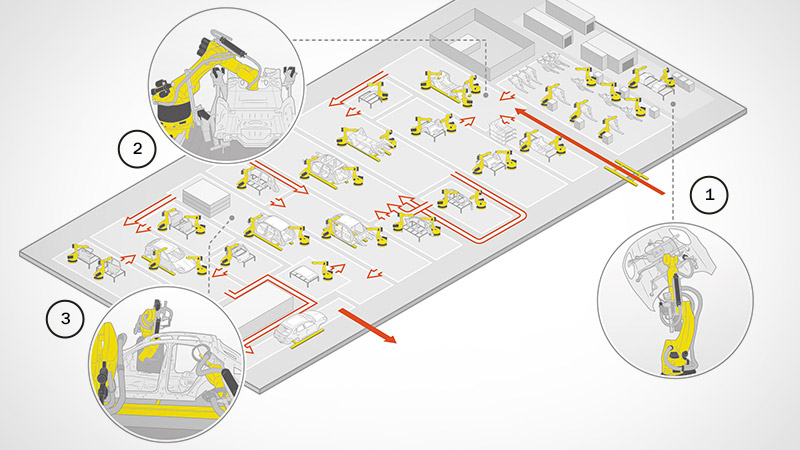
1 Fabrication du capot moteur
Le capot moteur en aluminium du
2 Plancher
C’est là que naît le
3 Caisse
La première étape est la création du dessous de caisse, puis l’assemblage de la caisse en blanc. Le bas de caisse reçoit alors les flancs et le toit.
Atelier de peinture

1 L’apprêt
La première couche de peinture est l’apprêt. Il existe dans trois couleurs (blanc, anthracite, bleu clair) et choisi en fonction de la peinture de finition qui doit le recouvrir.
2 Peinture de finition et vernis incolore
Après l’apprêt vient la peinture de finition, déclinée pour le
3 Tunnel Ergo Lux
Tous les
Ligne de montage
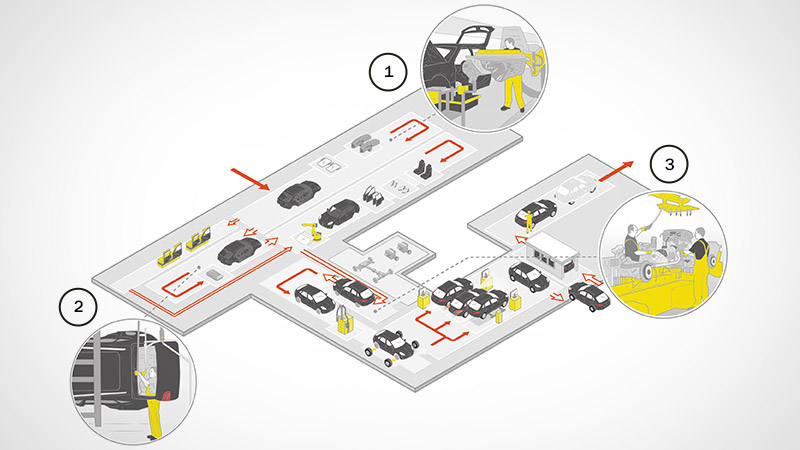
1 Montage du poste de conduite
Cette cadence sert à intégrer dans le véhicule l’un des plus gros modules complets : le poste de conduite. Les opérateurs exécutent ce travail de haute précision à l’aide d’un robot permettant de diriger le poste de conduite à l’intérieur du véhicule.
2 Balancelle rotative
Au bout de la ligne Intérieur, les véhicules passent de la plateforme élévatrice sur la balancelle rotative, pour un travail plus ergonomique au niveau du dessous de caisse et des zones difficiles à atteindre.
3 Union
C’est ici que sont assemblés les uns aux autres le châssis complet, la chaîne cinématique avec moteur et transmission et la carrosserie.