Perfekt gemacht
Der
Die Bodengruppe bittet zum Tanz. An der Station 1810 im neuen Karosseriebau des
Kurz zuvor war er noch eine Ansammlung einzelner Aluminium- und Stahlblechteile, von Lieferanten ins Versorgungszentrum Karosseriebau transportiert. Von dort gelangen sie per Routenzug taktgenau an die Anlagen im Werk. Anlagen, die in Rekordzeit aufgebaut wurden. In weniger als 26 Monaten entstanden nicht nur der Karosseriebau und die Lackiererei, auch die Montage hat
Mittlerweile hat der vorderste der drei Roboter seine Schweißzangen abgelegt und einen Handlingsgreifer aufgenommen, mit dem er den
Dieser Prozess beginnt im Volkswagen-Werk Bratislava in der Slowakei. Dort wird auf der größten Presse des VW-Konzerns auch die
Zurück in Leipzig. Die letzte Station im Karosseriebau, das Finish. Zwei Karosseriebauer kontrollieren Oberflächen und Anbauteile. „Die Fahrzeug-Geometrie muss stimmen, damit in der Montage alles perfekt passt“, erklärt Riediger. Von hier aus begeben sich die Karosserien in Richtung Lackiererei.
Galerie.
Das Werk Leipzig verbindet eine hochmoderne Serienfertigung mit der Exklusivität einer Manufaktur. Stichwort Individualisierung. „Zum Beispiel können wir jede vom Kunden gewünschte Außenfarbe lackieren“, sagt Roland Töpfer, der Leiter der Lackiererei, und ergänzt: „Dafür haben wir unser ,Sofa‘.“ Die Abkürzung steht für Sonderfarbsystem. Damit lassen sich Farbmengen für ein einziges Fahrzeug bereitstellen und gegebenenfalls die Farbe nach jedem Lackiervorgang wechseln.
Zunächst jedoch steht Tauchen auf dem Programm. In der Vorbehandlung zur Kathodischen Tauchlackierung (KTL) wird die Karosserie gereinigt und entfettet. Um alle Hohlräume zu erreichen, dreht sich der
Sind Schweißnähte und Flansche – die Verbindungsstellen – versiegelt, der Unterbodenschutz aufgetragen, wird es bunt. Füller, Basislack, Klarlack. In dieser Reihenfolge erhält der
Das
Auch der Ergo-Lux-Tunnel, eine mit sparsamen LED-Modulen bestückte Lichtröhre, passt in dieses Konzept. Unter dem extra gleichmäßigen Streifenlicht lässt sich die Lackierung optimal kontrollieren: Zwei Mitarbeiter prüfen mit konzentriertem Blick eine Haube und streichen – ohne Handschuhe – sanft darüber. Nur so können sie Unebenheiten erfühlen, die sie anschließend wegpolieren. Jetzt ist der
Es ist die spielerische Leichtigkeit, die einem hier als Erstes auffällt. Karossen schweben an Drehgehängen vorbei oder wandern via Hubtisch von einem Fertigungstakt zum nächsten. Elektrische Routenzüge kreuzen, versorgen die Montagelinien mit Material. Eine exakt abgestimmte Harmonie, die einer höheren Ordnung zu gehorchen scheint. Dahinter verbirgt sich das Perlenkettenprinzip: ein logistischer Prozess, der ohne Lagerhaltung auskommt und in der die Teile „just in time, just in sequence“, also zur richtigen Zeit in der richtigen Reihenfolge, ans Band gelangen. Doch nicht nur das System, auch die Mitarbeiter strahlen diese Leichtigkeit aus. Im Zuge der Werkserweiterung wurden 1500 Mitarbeiter eingestellt. Alle individuell qualifiziert und in die Mannschaft integriert. „Für
In der Montage warten 225 Takte auf den
Vor der Unterbodenlinie wechselt die Karosserie vom Hubtisch aufs Drehgehänge, „um das Arbeiten am Unterboden ergonomischer zu gestalten“, wie Montageleiter Dr. Martin Kahmeyer erklärt. Ein Prinzip des
Inzwischen hat der
Während die Karosserie per Gehänge einschwebt, nähern sich Fahrwerk und Antriebsstrang der Vermählung auf einem fahrerlosen Transportsystem (FTS). Die feierliche Vereinigung findet vollautomatisch statt. Trauzeugen sind die Mitarbeiter eine Station später, die die Federbeine in den dafür vorgesehenen Aufnahmen verschrauben. Zur Aussteuer gehört in der Folge das Befüllen mit Kraftstoff, Brems- und Kühlflüssigkeit sowie Motoröl. Am Ende der Mixlinie steht der
Dr. Oliver Blume kennt alle Prozesse der
Text: Thorsten Schönfeld
Fotografie: Stefan Warter
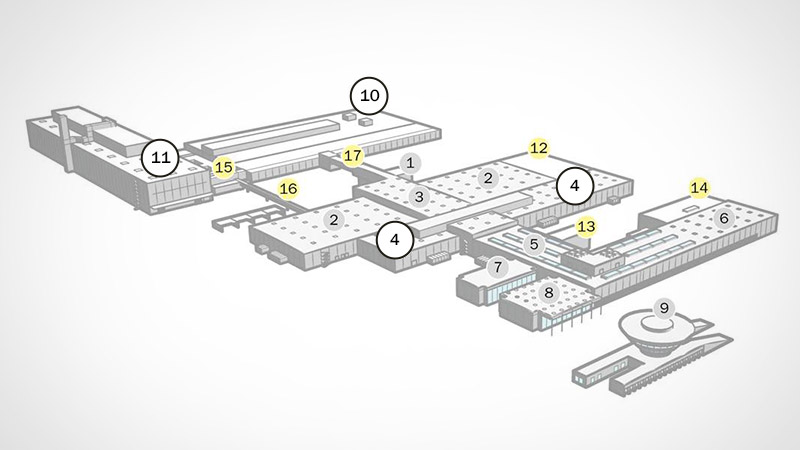
Kernwerk
1 Entladebahnhof
2 Versorgungszentrum
3 Entkopplungsmodul
4 Montagelinie
5 Endmontage
6 Pilot- und Analysezentrum
7 Casino
8 Integrationszentrum
9 Kundenzentrum
Neue Werksbereiche
10 Karosseriebau
11 Lackiererei
12 Erweiterung Versorgungszentrum
13 Neue Motor-Vormontage
14 Neue Finish-Linie
15 Integrationszentrum West
16 Fußgängerbrücke
17 Karosseriebrücke
Karosseriebau
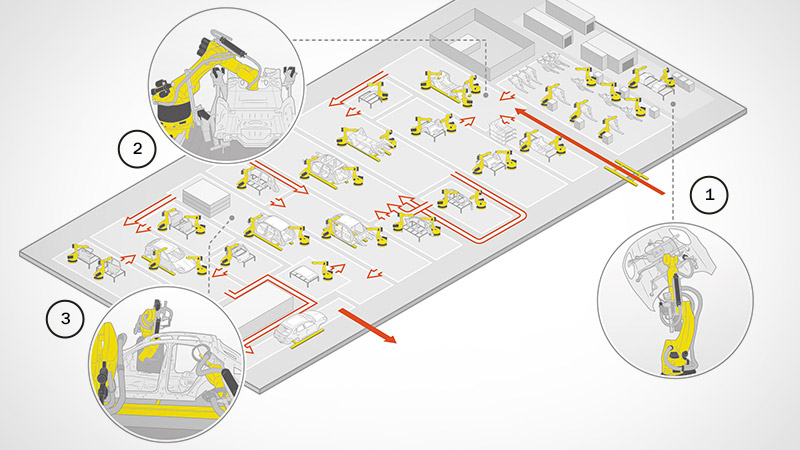
1 Fertigung der Motorhaube
Eine produktionstechnische Meisterleistung ist die Aluminium-Motorhaube des
2 Bodengruppe
Die Geburtsstätte des
3 Aufbau
Zuerst entsteht der Unterboden, danach der Aufbau. An dieser Stelle wird der Unterboden um die Seitenteile und das Dach ergänzt.
Lackiererei

1 Der Füller
Die erste Lackschicht ist der Füller, auch Grundierung genannt. Ihn gibt es in drei Farbtönen (Weiß, Anthrazit und Hellblau). Er wird auf den anschließend folgenden Decklack abgestimmt.
2 Decklack und Klarlack
Dem Füller folgt der Decklack und damit eine von elf für den
3 Ergo-Lux-Tunnel
Zur Lackkontrolle durchlaufen alle
Montage
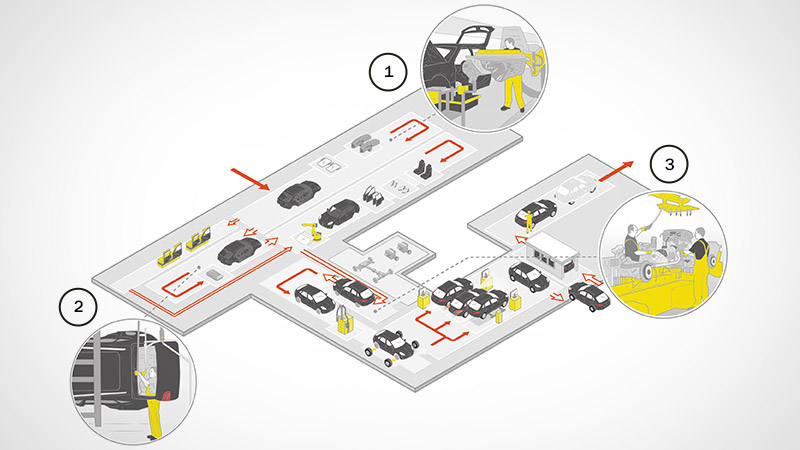
1 Einbau des Cockpits
Eines der größten Komplettmodule wird bei diesem Takt in das Fahrzeug integriert: das Cockpit. Die Montage-Mitarbeiter erledigen diesen Präzisionsjob mit einem Handlinggerät, an dem das Cockpit in das Fahrzeug dirigiert wird.
2 Drehgehänge
Am Ende der Interieurlinie wechseln die Fahrzeuge vom Hubtisch aufs Drehgehänge, um das Arbeiten an Unterboden und schwer zugänglichen Bereichen ergonomischer zu gestalten.
3 Hochzeit
Hier werden das komplette Fahrwerk, die Antriebstechnik mit Motor und Getriebe, und der komplette Aufbau miteinander verschraubt.