Einen Gang zurückschalten. Durchblättern und abtauchen.
Exklusiv, einzigartig, inspirierend: Der Christophorus ist das Magazin für Porsche-Enthusiasten. Und fast so alt wie die Sportwagenmarke selbst: Seit der ersten Ausgabe im Jahr 1952 begeistert die Publikation ihre Leser mit Geschichten rund um das Unternehmen Porsche – mit Persönlichkeiten, Produkten, Historie und Motorsport.
Die Print-Ausgabe des Porsche-Magazins erscheint weltweit viermal pro Jahr in 11 Sprachen mit einer Auflage von rund 600.000 Exemplaren pro Ausgabe. Der Christophorus gilt als eines der renommiertesten Unternehmensmagazine weltweit. Historische Exemplare haben großen Sammelcharakter.
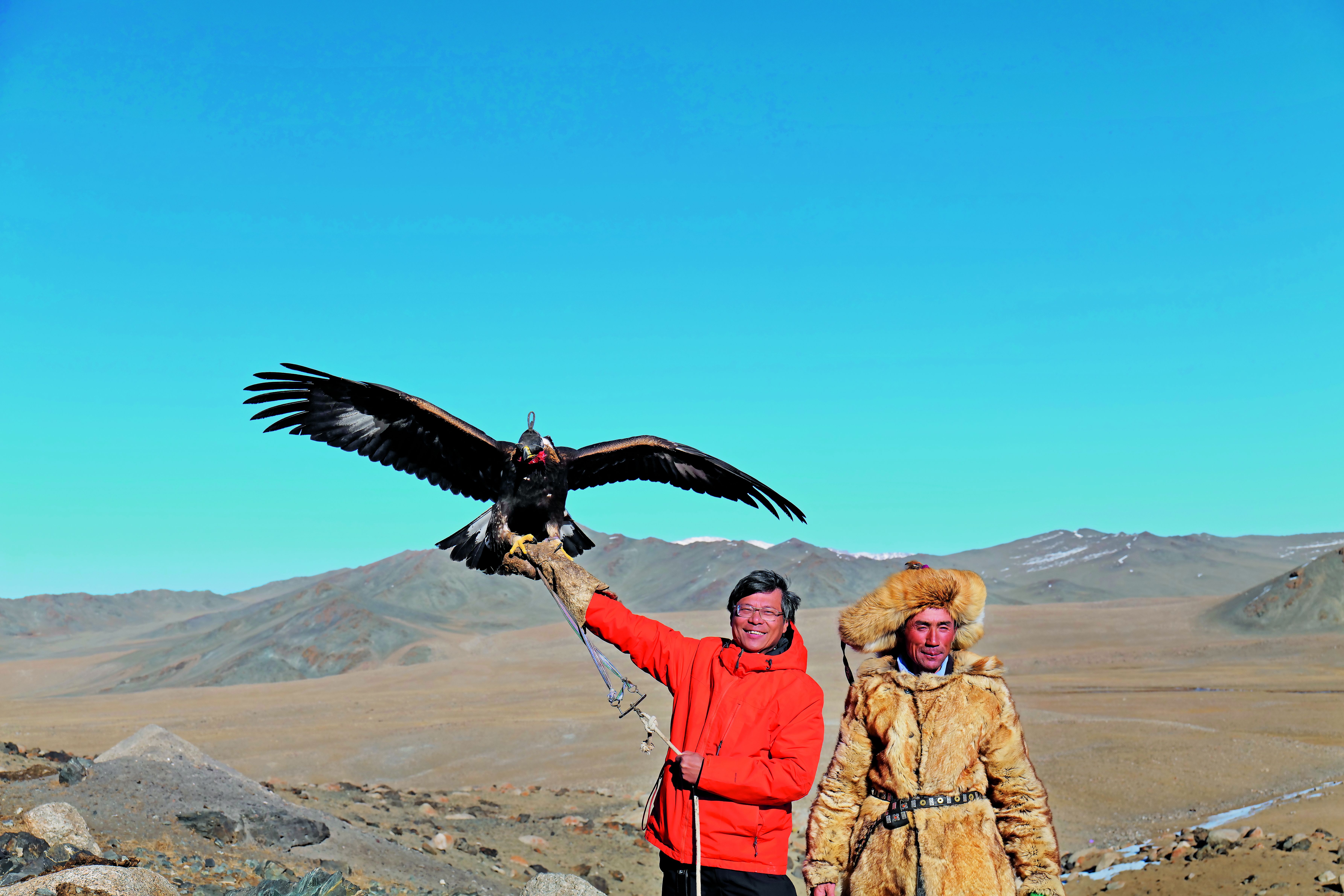
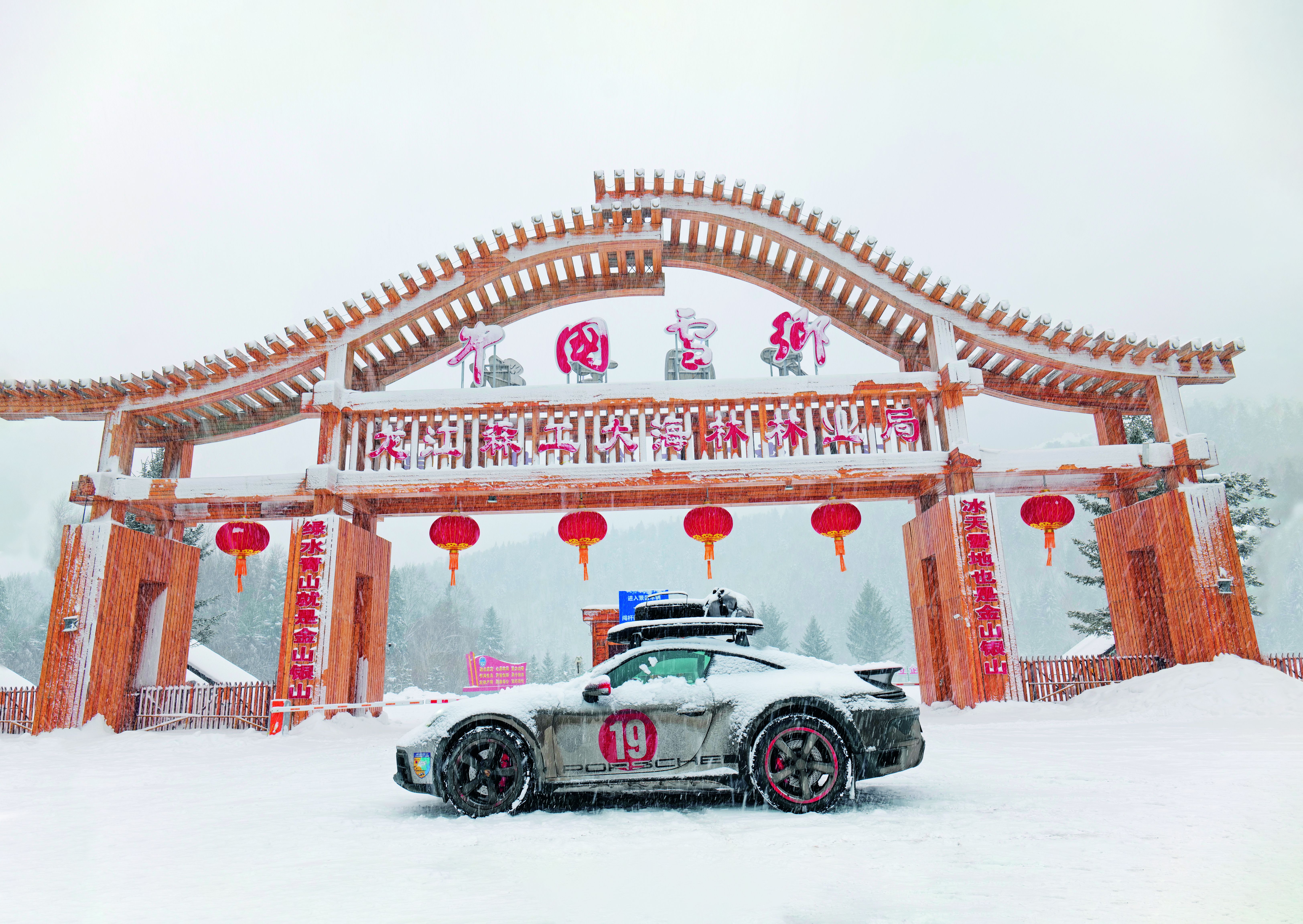

Ausgabe #413
Tagebuch aus der Wüste.
Von minus 20 bis plus 38 Grad Celsius, von der Küste bis auf fast 4.700 Meter Höhe, vom Highway bis zur Geröllpiste: Nguyen Hoang Anh, Inhaber eines Logistikunternehmens, fuhr in seinem 911 Dakar von Vietnam über China bis in den mongolischen Teil der Wüste Gobi – und zurück.
9:11 das Videomagazin

Abonnement abschließen
Jährlich erscheinen vier Ausgaben des Christophorus, die in einem Abonnement für 24 Euro erhältlich sind.