Einen Gang zurückschalten. Durchblättern und abtauchen.
Exklusiv, einzigartig, inspirierend: Der Christophorus ist das Magazin für Porsche-Enthusiasten. Und fast so alt wie die Sportwagenmarke selbst: Seit der ersten Ausgabe im Jahr 1952 begeistert die Publikation ihre Leser mit Geschichten rund um das Unternehmen Porsche – mit Persönlichkeiten, Produkten, Historie und Motorsport.
Die Print-Ausgabe des Porsche-Magazins erscheint weltweit viermal pro Jahr in 10 Sprachen mit einer Auflage von rund 600.000 Exemplaren pro Ausgabe. Der Christophorus gilt als eines der renommiertesten Unternehmensmagazine weltweit. Historische Exemplare haben großen Sammelcharakter.
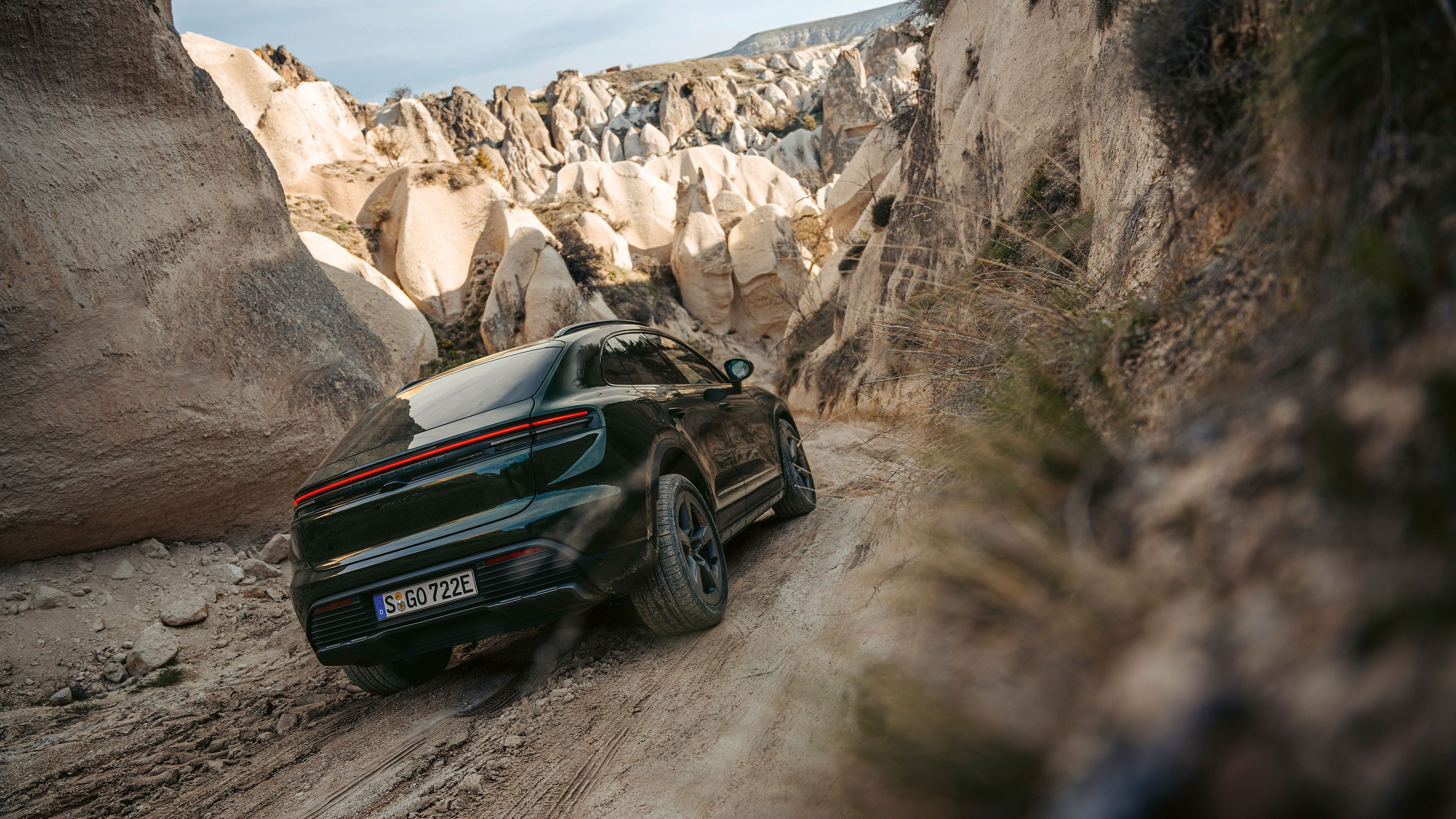
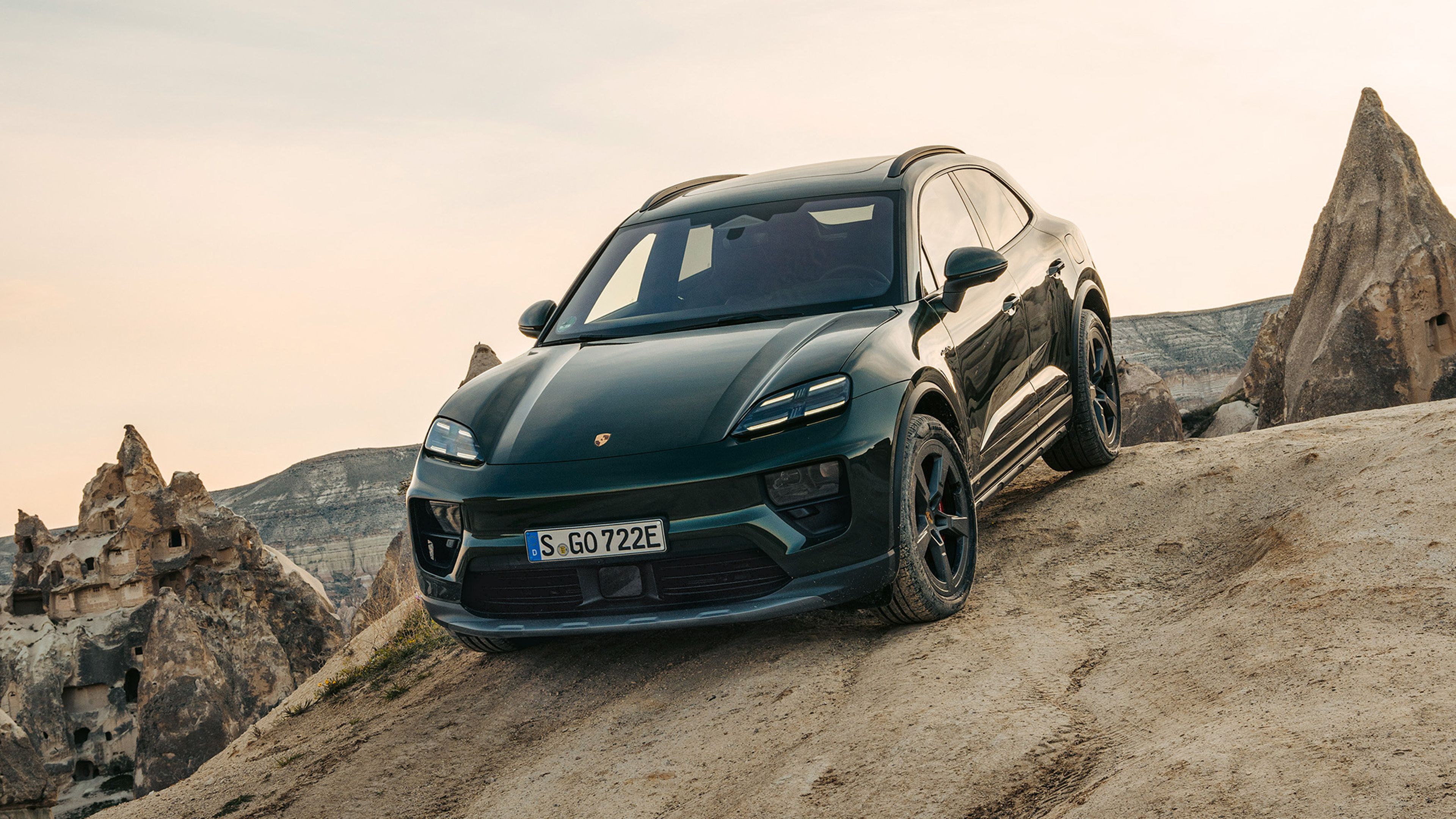

Ausgabe #415
Abseits des Asphalts
Skurrile Felsen, bunte Heißluftballons, uralte Höhlen und kulinarische Köstlichkeiten – Kappadokien bietet eine beeindruckende Kulisse. Mit dem neuen Macan 4S erkunden wir die angesagte Region der Türkei – und zwar überwiegend im Offroad-Modus.

Abonnement abschließen
Jährlich erscheinen vier Ausgaben des Christophorus, die in einem Abonnement für 24 Euro erhältlich sind.