Scalare una marcia. Sfogliare. Perdersi.
Esclusivo, straordinario, suggestivo: Christophorus è la rivista per gli appassionati di Porsche. E ha quasi la stessa età del brand di auto sportive: sin dalla sua prima edizione, uscita nel 1952, la pubblicazione entusiasma i suoi lettori con racconti incentrati su Porsche, che vedono protagonisti personaggi famosi, prodotti, storia e Motorsport.
La versione cartacea del Porsche Magazin viene pubblicata in tutto il mondo quattro volte all’anno in 11 lingue, con una tiratura di circa 600.000 esemplari per numero. Christophorus è una delle riviste aziendali più rinomate al mondo. Gli esemplari storici sono molto ambiti dai collezionisti.
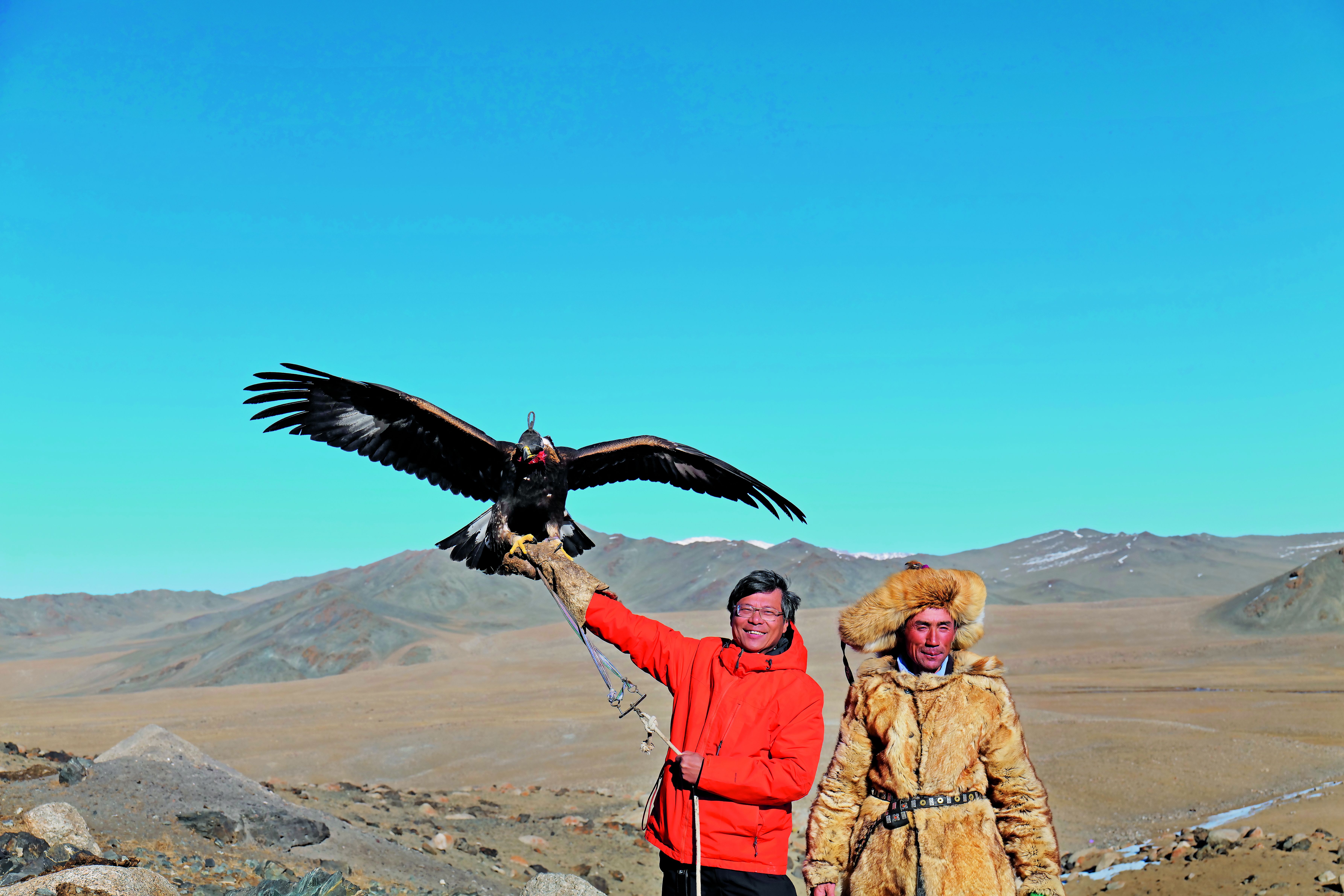
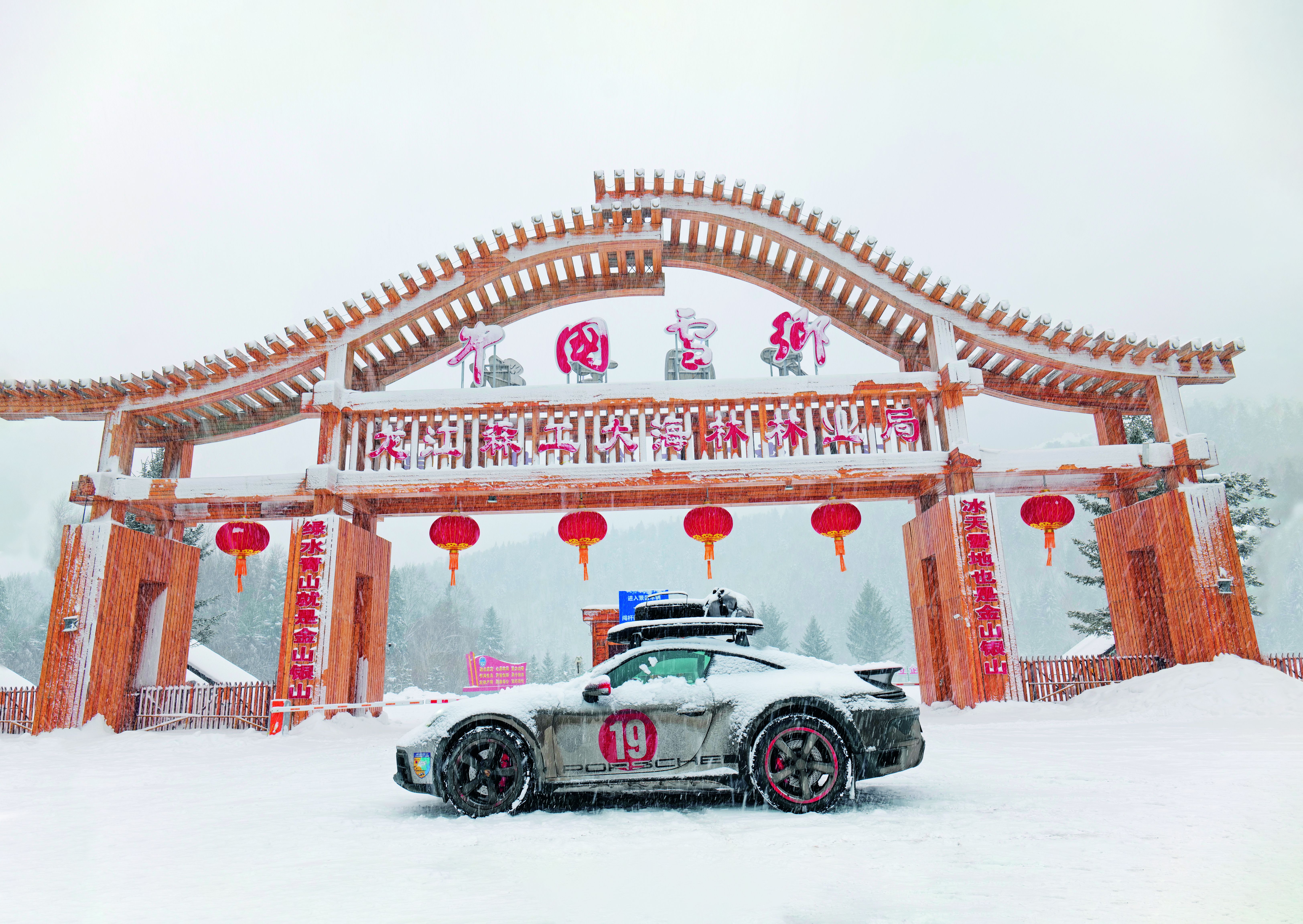

N° 413
Diario dal deserto.
Da meno 20 a più 38 gradi Celsius, dalla costa a quasi 4.700 metri di altitudine, dall’autostrada allo sterrato: Nguyen Hoang Anh, titolare di una società di logistica, ha guidato la sua 911 Dakar dal Vietnam, attraverso la Cina, fino alla parte mongola del deserto del Gobi.
9:11 – La rivista video

Abbonarsi
Ogni anno vengono pubblicati quattro numeri di Christophorus, disponibili in abbonamento al costo di 24 euro.