一つ戻る。ページをめくり没入。
エクスクルーシブ、ユニーク、インスピレーションたっぷり。クリストフォーラスは、ポルシェ愛好家のための雑誌です。その歴史はポルシェそのものと同じくらい長いものです。1952年の発刊以来、ポルシェという企業、そしてこの企業を形作ってきた人々、製品、歴史、モータースポーツなど、様々なストーリーをとりあげながら読者を魅了し続けています。
紙媒体によるポルシェマガジンは、世界中で毎年4回、毎号約60万部、11の言語で刊行されています。クリストフォーラスは、世界有数のカンパニーマガジンとみなされており、バックナンバーはコレクターアイテムとしても愛され続けています。
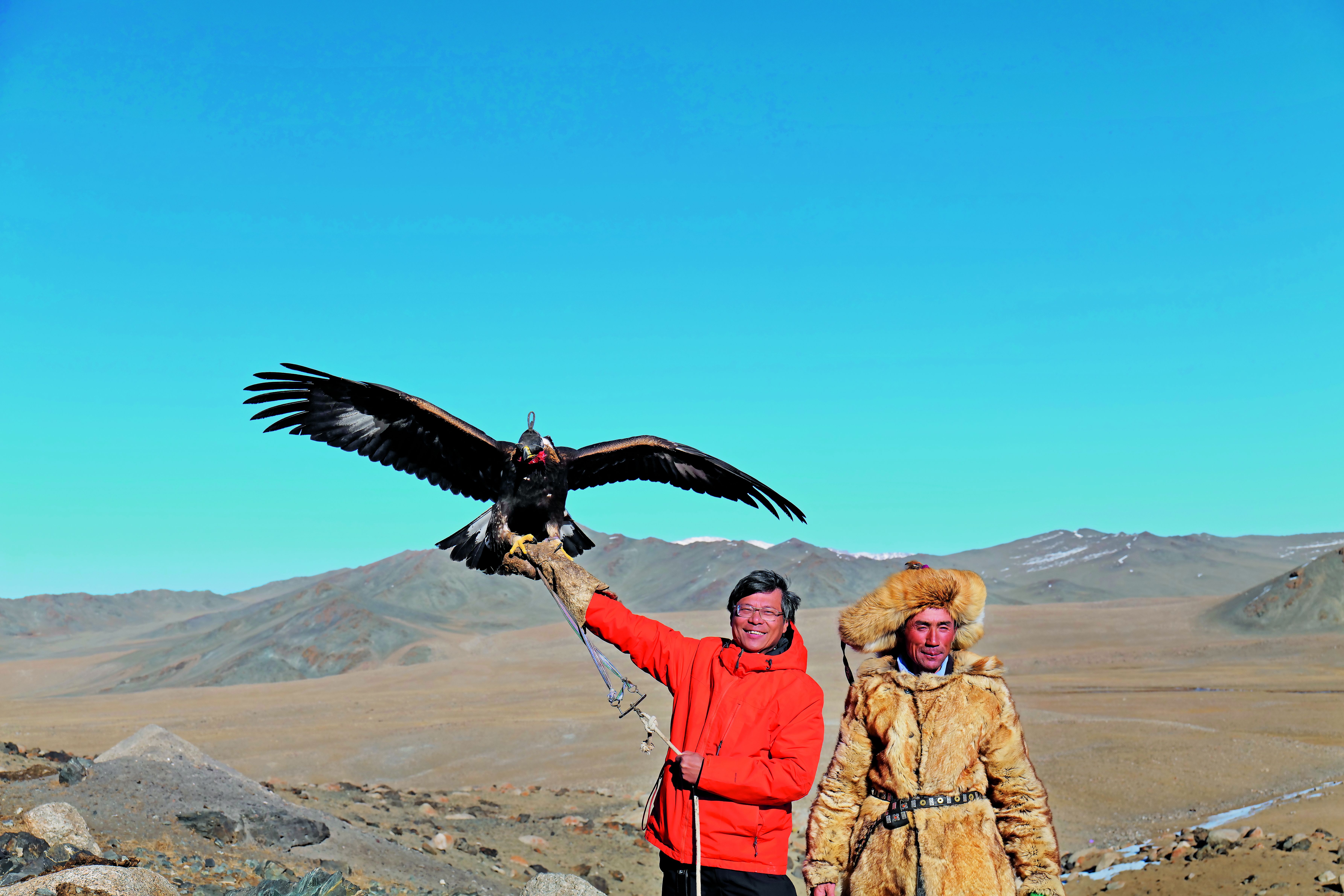
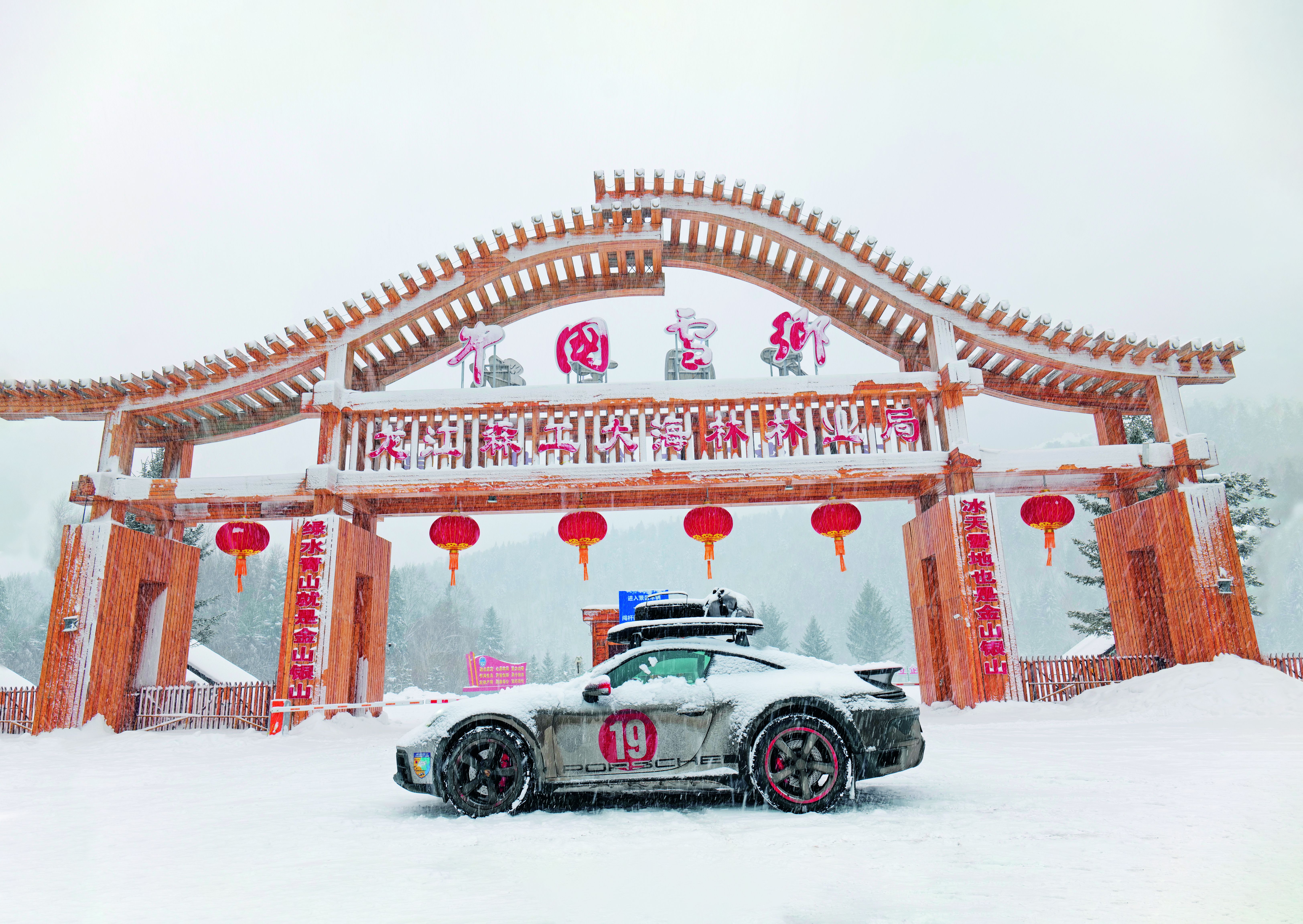

Nº413
砂漠のダイアリー。
マイナス20度からプラス38度まで、海岸から標高4700メートルまで、高速道路から砂利道を。物流会社のオーナーであるグエン・ホアン・アインは、911ダカールのハンドルを握りベトナムから中国経由でモンゴル部分のゴビ砂漠までを往復した。
9:11 ビデオマガジン

定期購読のお申し込み
季刊クリストフォーラスを24ユーロで定期購読。