Bajar las revoluciones. Hojear y sumergirse.
Exclusiva, única, inspiradora: Christophorus es la revista para los entusiastas de Porsche. Y tiene casi tanta historia como la propia marca de deportivos ya que, desde que salió el primer número en 1952, la publicación entusiasma a sus lectores hablando sobre personajes, productos, historia y automovilismo en torno a la empresa Porsche.
La edición impresa de la revista de Porsche se publica en todo el mundo cuatro veces al año en once idiomas con una tirada de unos 600 000 ejemplares por número. Christophorus está considerada una de las revistas de empresa más prestigiosas del mundo. Los ejemplares históricos tienen un gran valor para los coleccionistas.
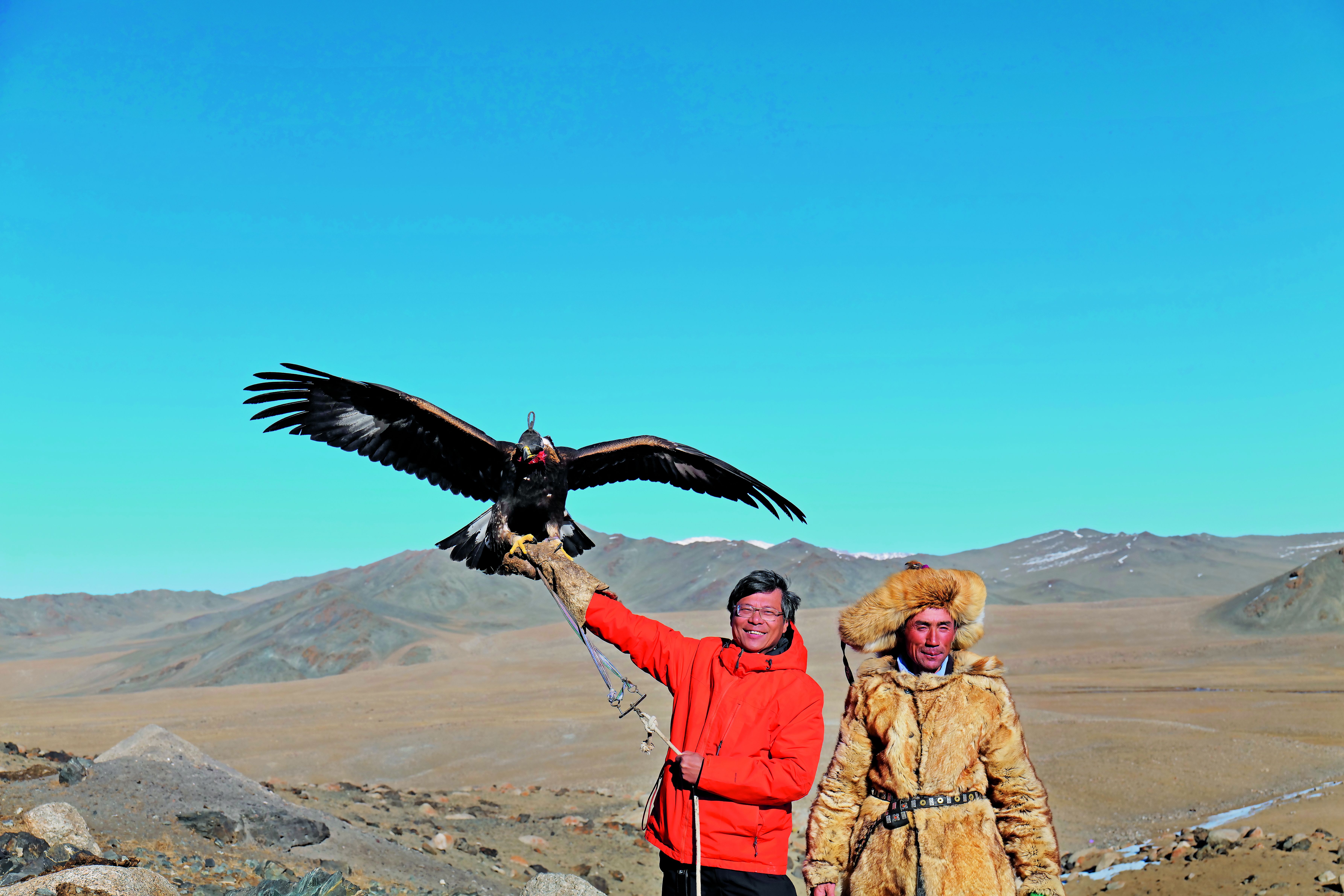
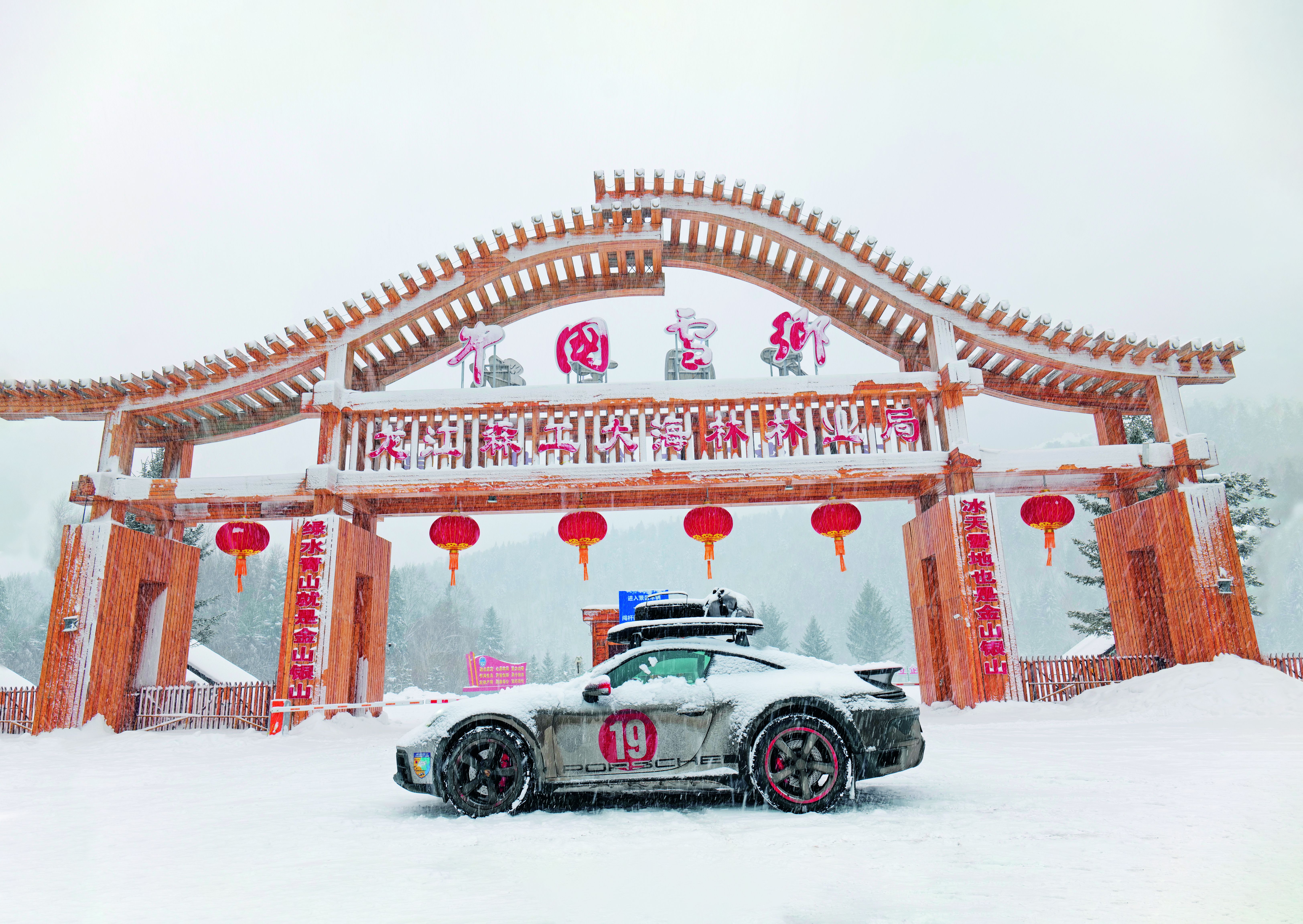

Número 413
Diario desde el desierto.
Desde 20 °C bajo cero hasta 38 °C, desde la costa hasta casi 4700 metros de altitud, desde la autopista hasta la pista de grava.
9:11, la revista en vídeo

Suscribirse
Cada año se publican cuatro números de Christophorus, disponibles mediante suscripción por 24 euros.